Types of Primary Sedimentation Tanks
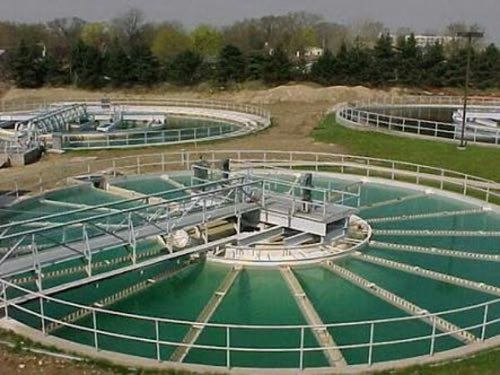
Primary Sedimentation takes place in the sedimentation tanks with the objective to remove readily settleable solids and floating materials and thus reduce the suspended solids content. The removal rate is 50-70% of suspended solids and 25 - 40% of BOD whereas, generally more than two rectangular or circular tanks are used.
Primary sedimentation tanks, also known as primary clarifiers or settling tanks, are an essential component of wastewater treatment plants. Their primary function is to remove settleable and floatable solids from the influent wastewater through the process of sedimentation.
Types of Primary Sedimentation Tanks
There are several types of primary sedimentation tanks commonly used in wastewater treatment systems, each with its own design characteristics and advantages.
Rectangular Horizontal Flow Tanks
Rectangular sedimentation tanks have a rectangular shape and are widely used in smaller wastewater treatment plants and decentralized systems. They are typically made of concrete or steel and have a series of baffles to promote settling and prevent short-circuiting of the flow. The effluent is collected through weirs or effluent launder channels. Rectangular sedimentation tanks are relatively simple in design and construction, making them cost-effective for smaller applications.
These are most commonly used for primary sedimentation, since they:
- Occupy less space than circular tanks.
- They can be economically built side-by-side with common walls.
- Length ranges from 15 to 100m and width from 3 to 24m (length/ width ratio 3:1 to 5:1)
- The maximum forward velocity to avoid the risk of scouring settled sludge is 10 to 15 mm/s (06 to 09m/min or 2 to 3 ft/ min), indicating that the ratio of length to width l/w should referrals be about.
- The maximum weir loading rate, to limit the influence of draw-down currents, is preferably about 300 m3/d-m, this figure is sometimes increased where the design flow is great than 3 ADWF.
- Inlets should be baffled to dissipate the momentum of the incoming flow and to assist in establishing uniform forward flow.
- Sludge is removed by scraping it into collecting hoppers at the inlet end of the tank.
- Some removal is essential in primary sedimentation tanks because of the grease and other floating matter which is present in wastewater. The sludge serapes can return along the length of the tank a the water surface. As they move towards the outlet end of the bank, the flights then move the sum towards a skimmer located just upstream of the effluent weirs.
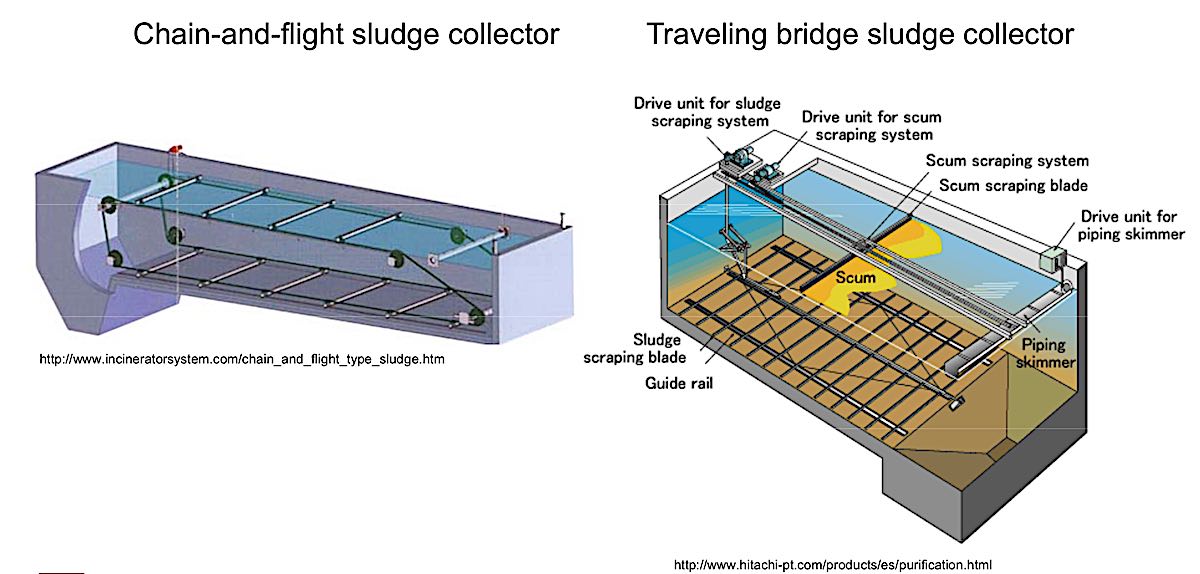
Circular Radial Flow Tanks
Circular sedimentation tanks have a circular shape and are commonly used in larger wastewater treatment plants. They are usually made of concrete and have a central inlet and a peripheral outlet to facilitate the flow pattern. The circular shape allows for more efficient removal of solids and improved flow characteristics compared to rectangular tanks. Circular sedimentation tanks are also equipped with mechanisms such as scraper blades or suction devices to remove settled sludge. These are also used for primary sedimentation.
-
Most common CRF Tanks have diameters from 3 to 60 m (side water depth range from 3 to 5 m)
-
Careful design of the inlet stilling well is needed to activate a stable radial flow pattern without causing excessive turbulence in the vicinity of the central sludge hopper.
-
The weir length aroid the perimeter of the tank is usually sufficient to give a sates factory weir loading rate at maximum flow, but at low flows, very low flow depths may result.
-
To overcome the sensitivity of these tanks to slight errors in weir level and wind effects, it is common to provide v-much wares.
-
Sludge removal is effected by means of a rotary sludge scrapper who moves the sludge into a central hopper, from which it is drowned.
-
Scum removal is carried out by a surface skimming board attached to the sludge scrapper mechanism and positioned so that scum is moved towards a collecting hopper at the surface.
Up Flow Tanks:
-
Up-flow tanks, usually square in plan and with deep hopper bottoms, are common in small treatment plants.
-
Their main advantage is that sludge removal is cared out entirely by activity and no mechanical parts are required for cleaning them.
-
The steeply sloping sides usually horizontal concentrate the sludge at the bottom of the hopper.
-
Weir loading rate is a problem only at low flows. So v-match weirs are desirable.
-
The required up-flow pattern is maintained by weir troughs.
-
True-up flow tanks have a disadvantage in that hydraulic overloading may have more serious effects than in horizontal flow tanks.
-
Any practical with a velocity lower than VP = Q/A will not be removed in an up-flow tank but will escape in the effluent.
-
In a horizontal flow tank assuming that such particles were uniformly distributed to the flow, particles with Vp=Q/A still be removed in proportion.
Square Sedimentation Tank
They may be flat-bottomed or hopper-bottomed. Wastewater enters the tanks, usually at the center, through a well or diffusion box. The tank is sized so that retention time is about 24 (range 20 minutes to 3h). In the quiescent period, the suspended part ides settle to the bottom as sludge and are raked towards a central hopper from where the sludge is withdrawn.
Primary sedimentation is among the oldest wastewater treatment process. Traditionally the design criteria for sizing setting tanks are:
Average overflow rate: 30 - 50 m3/m2/d (Typical 40 m3/m2/d) [800-1200 gal/ft2-d (Typical 1000 gal/ft2-d]
Peak hourly overflow rate: 50 - 120 m3/m2/d (Typical 100 m3/m2/d) [2000-3000 gal/ft2-d (Typical 2500 gal/ft2-d]
Weir loading rate: 1.5 - 2.5h (Typical 2.0 h) [1.5 - 2.5 h (Typical 2.0h)]
Rectangular Sedimentation Tanks |
Circular Sedimentation Tanks |
|
Depth |
10-16 ft (Typical 14) 3 - 3.9 m (Typical 4.3) |
10-6 (Typical 14) 3.39m (Typical 4.3 m) |
Length |
50-300 ft (Typical 80-30 ft) |
Diameter 10-200 (Typical 40-150ft) 3-60 m (Typical 12-45m |
Flight speed |
2-4 ft/min (Typical 3 ft/min) or (Typical 0.9 m/min) |
Scraper’s speed 0.02-0.05/min (Typical 0.03 Rev/min) |
Bottom Slope |
1in/ft or Typical 0.9m/m check |
1.12 ft |
- Always provide a minimum of 2 sedimentation tanks.
- Sludge accumulation is the same for both.
- Sludgy accumulation of 2.5 kg of wet solids per m3 of flow.
Design and Sizing of Primary Sedimentation Tanks
The design and sizing of primary sedimentation tanks involve various calculations, including hydraulic loading rate, settling velocity, surface area, and detention time. Here are a few equations commonly used in the design process:
Hydraulic Loading Rate (HLR):
HLR = Q / A
where HLR is the hydraulic loading rate (m3/m2/day), Q is the flow rate (m3/day), and A is the surface area of the tank (m2).
Detention Time (T):
T = V / Q
where T is the detention time (hours), V is the effective volume of the tank (m3), and Q is the flow rate (m3/h).
These equations help determine the appropriate size and dimensions of the sedimentation tank based on the influent flow rate and desired settle characteristics.